
TESTING AND IMAGING SERVICES
'They don't build them like they used to' We've all heard this before, and it probably rings the most true when it comes to buildings. Have you ever stood next to an old, inefficient window in the middle of winter and felt a draft of cold air? Air can leak through the envelope in a myriad of ways, through thermal weak points in the structure, windows with low thermal resistance, plumbing and ventilation stacks, kitchen/dryer vents and even through electrical sockets.
Infiltration can account for 40 of the heating load in older homes. Even in new construction, efficiency losses as a result of air leakage can be responsible for 25 percent of the total heat loss in the new house. We've made progress, but standard construction practices still have a lot of ground to make-up. Certification programs like Passive House, R-2000, LEED, EnerPHit and even building codes have set metrics in place to limit air changes due to infiltration.
At ZON, we understand that designing a tight envelope is only half of the equation. The rubber really hits the pavement when it comes to construction and field verification of the building envelope to ensure that all weak points have been properly insulated and sealed. Our team includes several field specialists that are experienced in various field testing techniques for both buildings and solar photovoltaic arrays.
AIR TIGHTNESS TESTING
To evaluate the effectiveness of a building's air barrier system, an airtightness test measures how easy it is for air to leak through the enclosure. Air leaking out of the building enclosure causes a considerable amount of energy to be consumed as make-up air needs to be condition to account for the leakage rates. Air leakage through the building enclosure also increases the risk of condensation through the building envelope, as well as the increased risk of polluted air (e.g. from a parking garage) being introduced into the building.
Given the potential energy savings, improved indoor air quality, reduced condensation risk and overall improved understanding of HVAC equipment loads, it is no wonder that building codes and third-party environmental rating systems such as LEED, R2000 and Passive House have implemented airtightness targets and testing metrics into their standards.

Air Tightness or "Blower Door" tests are conducted by using large fans to extract or supply air to the building and measuring the corresponding pressure differential across the building enclosure. Prior to testing, care should be taken to ensure that penetrations through the envelope are adequately sealed, including intake and exhaust ducts, line set sleeves, plumbing drainage and vent pipes, and electrical and communication conduits.
Following the test, ZON Engineering Inc. will provide a site report that identifies deficiencies and areas for improvement, as well as the measured air changes per hour (ACH) at 50 Pa (pressurization and depressurization), the air flow rate (cfm and/or L/s) at 50 Pa, and the equivalent leakage area through the envelope. These metrics can then be used to improve envelope deficiencies prior to re-testing.
INFRARED (IR) THERMOGRAPHY TESTING
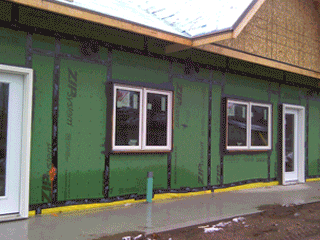
The purpose of infrared thermography is to identify and document areas of the building enclosure that display abnormal infrared radiation patterns that may indicate current or future failure/problems. By doing so, targeted repairs can be made to restore the integrity of the enclosure with the end goal of extending the building life, avoiding high-cost repairs in the future, improving comfort, increasing durability and reducing energy consumption.
Thermal Imaging & Infrared Thermography can assist in identifying:
-
Heat Loss and Air Infiltration
-
Missing and Damaged Insulation and Voids in the Building Envelope
-
Hidden Roof Leaks
-
Energy Efficiency Concerns
-
"Hot Spots" in Electrical Equipment, including Solar Modules and Distribution Equipment
ZON Engineering Inc. has Level I Certified Thermographers on staff that have completed the necessary training through the Infrared Training Centre (ITC) in Burlington, ON. ITC is an ISO-9001 registered company and is accredited in IR thermography training by the International Electrical Testing Association (NETA).
Infrared Thermography is a non-destructive testing technique used to measure and map surface temperatures of various building elements. All objects emit electromagenetic radiation of a wavelength dependent on the object's temperature. This radiation can be measured with infrared imaging equipment which interprets the variations as different colours in the thermal image. As a testing technique, it is accurate, repeatable, economical and it does not require any modification to the building or inconvenience to the public.